In the now revitalized Navy Yard, a historic site is returned to its manufacturing glory
By James Tate
Brooklyn’s Navy Yard Building 128 had been empty and in disrepair for more than twenty years when Industry City CEO Andrew Kimball, then-president of the Navy Yard, approached developer David Belt in 2011 with an opportunity to bring the massive former machine shop back to life. Once a thriving center of ship manufacture, Building 128 serviced the U.S. military in both World Wars before falling into neglect in the second half of the twentieth century, along with much of the rest of the 300-acre Navy Yard. Belt, founder of the firm Macro Sea and with a long background in shepherding the city’s historic buildings into the modern day, was inspired by the site’s grandeur, and with partner Scott Cohen set about developing a plan to use Building 128 to provide a large-scale community for cutting-edge manufacturing.
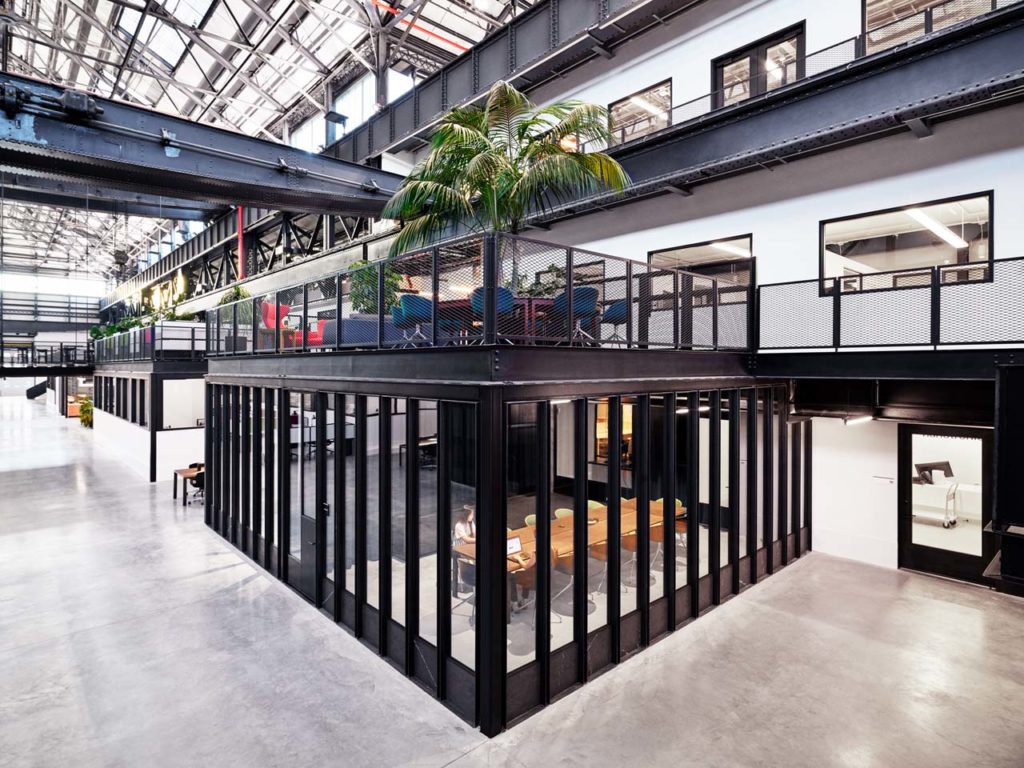
HyperFocal: 0
Five years later, New Lab was born, a public-private partnership committed to the design of robotics, artificial intelligence, additive manufacturing (such as 3D printing), and nanotechnology. With 84,000 square feet and nearly 80 companies under its roof, its mission is to provide a home and resources for NYC based engineers and entrepreneurs.
“[New technology] doesn’t roll off the tongue when you think of New York,” said New Lab media manager Molly Erman. “It’s not fashion or finance or publishing…we’re hoping to give Silicon Vally a little bit of a run for its money.” Its specific interest in purposeful hardware, “not tech for tech’s sake” as Erman said, offers a good argument for its placement here. “Having access to New York’s other industries and being able to liase directly with the city government makes sense.”
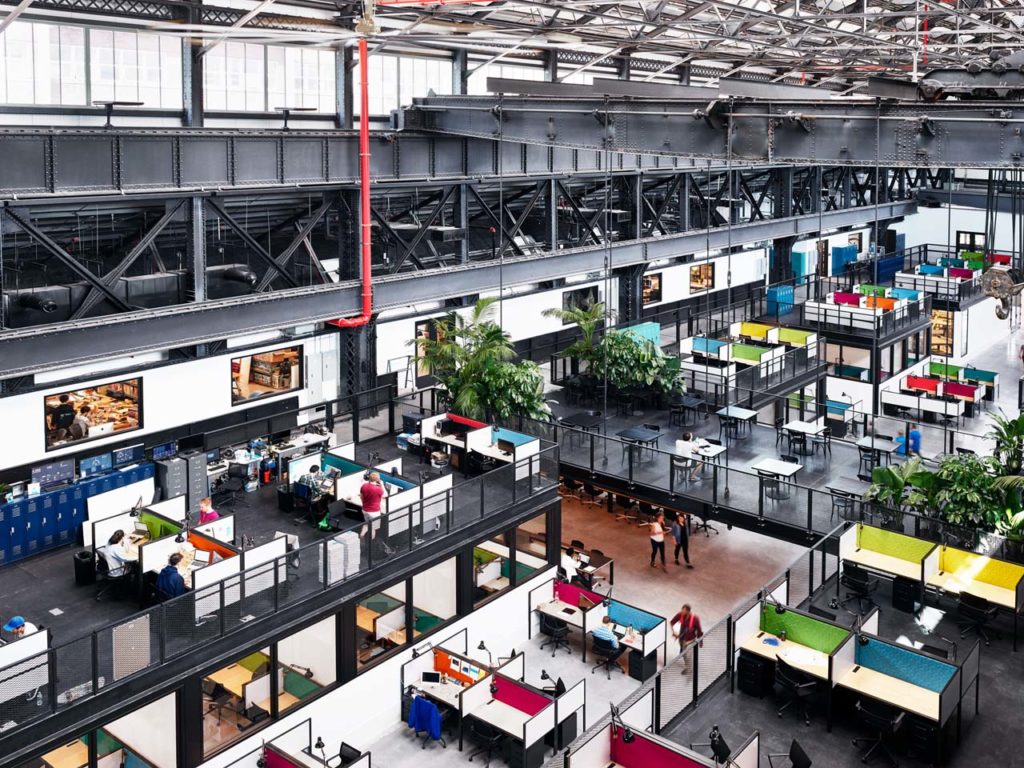
HyperFocal: 0
The mission overall is to facilitate an “optimistic view” of the future of technology, explained Erman. “We’re not seeking companies that want to come in and automate all of the jobs currently being done by humans, but instead are looking at ways for the work humans do to be assisted by technology to work smarter.” Tenants in the enormous, two-story facility are selected for business endeavors that are “genuinely positioned to benefit humanity,” and with an aim to outgrow New Lab’s facility within two to three years. “Ideally we’d like to see our companies graduate and take on space in the Navy Yard and become our neighbors. A big part of what this business is based on is the history of this building, as, circa 1915, it represented the future of manufacturing for New York City. Now that it’s 2017, we want to be a hub for that as well.”
Building 128 was transformed by Macro Sea from its World War-era condition to its present state in just under a year. “51,000 square-feet became 80,000,” said Erman, “and was expanded in a historically accurate way, something that was important to us. We added an entire second floor based on bridges suspended from the original gantry cranes that run across the roof. The cranes are the root of three bridges that unite the mezzanine.” Another of Macro Sea’s restorations is St. Ann’s Warehouse in DUMBO, not far from New Lab (see the story “Saintly Endeavors” in this issue), an abandoned tobacco warehouse converted into a performing arts center. “It was that project that caught the eye of Andrew Kimball, who personally asked David to check out this building, because it’s a big space and no one was really sure what to do with it.”
Having discovered an ideal home for New Lab, Belt, who is its acting CEO, turned to the question of the company’s ambitions.
“All of the tenants here are late-stage startups with a solid foundation of funding, so we don’t see ourselves as an incubator,” Erman said. “For our members, this is an independent place—we don’t take any IP [intellectual property], we take active steps to make sure that we’re accepting companies that aren’t in competition with one another, and that can only benefit from adjacencies.” Belt thinks of it as a Noah’s Ark—a healthy mix of companies doing a variety of work rather than a co-working space.
“We’re really a lab, with shared resources,” the media manager added. “For that reason, we don’t have red wine on tap or a ping-pong table or a nap room; it’s a professional environment where people are serious about getting work done.”
Those people comprise an array of innovators whose output ranges from robotics used in NASA’s Mars rovers (Honeybee Robotics) to miniature hydroponic farms (Farmshelf). Then there’s Buoy
Health, which produces a digital tool that uses AI to help consumers diagnose medical symptoms—an unusual instance of an entirely software-based tenant.
“Sometimes we break our own rules,” laughed Erman. “At our core, we’re hoping to service a community of people who are working in hardware, because it’s the hardest thing to do in New York City. It’s much easier to build an app in Manhattan than it is to solder something or prototype something in the middle of the day. Honeybee at one point had been working above a popular bar in the Lower East Side, so upstairs from kids chugging pickle backs there were engineers working on pieces of a Mars rover. That’s an amazing juxtaposition, so when we were building New Lab, that was a big part of our thesis. Previously, these companies were scattered all over, and we hear feedback from our companies all the time that it’s amazing to have access to like-minded people that you can share information with and just relate to. This is a great community doing hard things in a hard place, and David and Scott were excited about filling that need.”
New Lab
19 Morris Avenue / 718.488.7005 / newlab.com